- Equipment
- HC65
HC65
HC65
Details
Key Features and Benefits
- Constructed entirely from stainless steel & Acetal co-polymer
- Convenient, detachable infeed for intensive cleaning
- 4 sets of configurable seam crimps
- Auto stoppage function to prevent seal degradation
- Configurable infeed to suit application
- Rotary end-crimp configurable to suit application
- 20 – 400 packs per min.
- 100 product settings
- Pictorial stoppage diagnostics with corrective action pop-ups
Visit Redpack at www.redpack.co.uk for more information.
See all Fox Solutions equipment for advanced automation in fresh produce packaging.
Works With
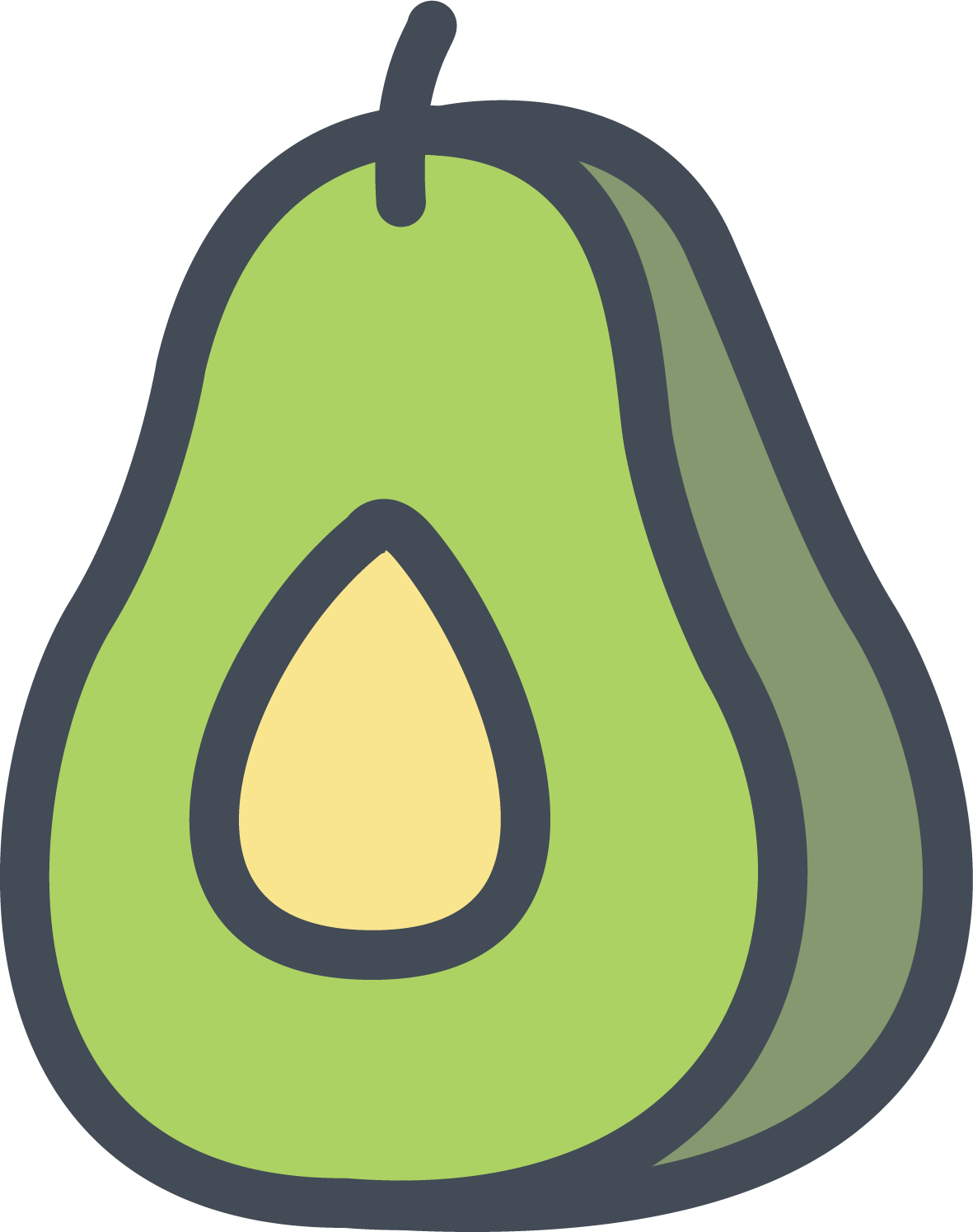
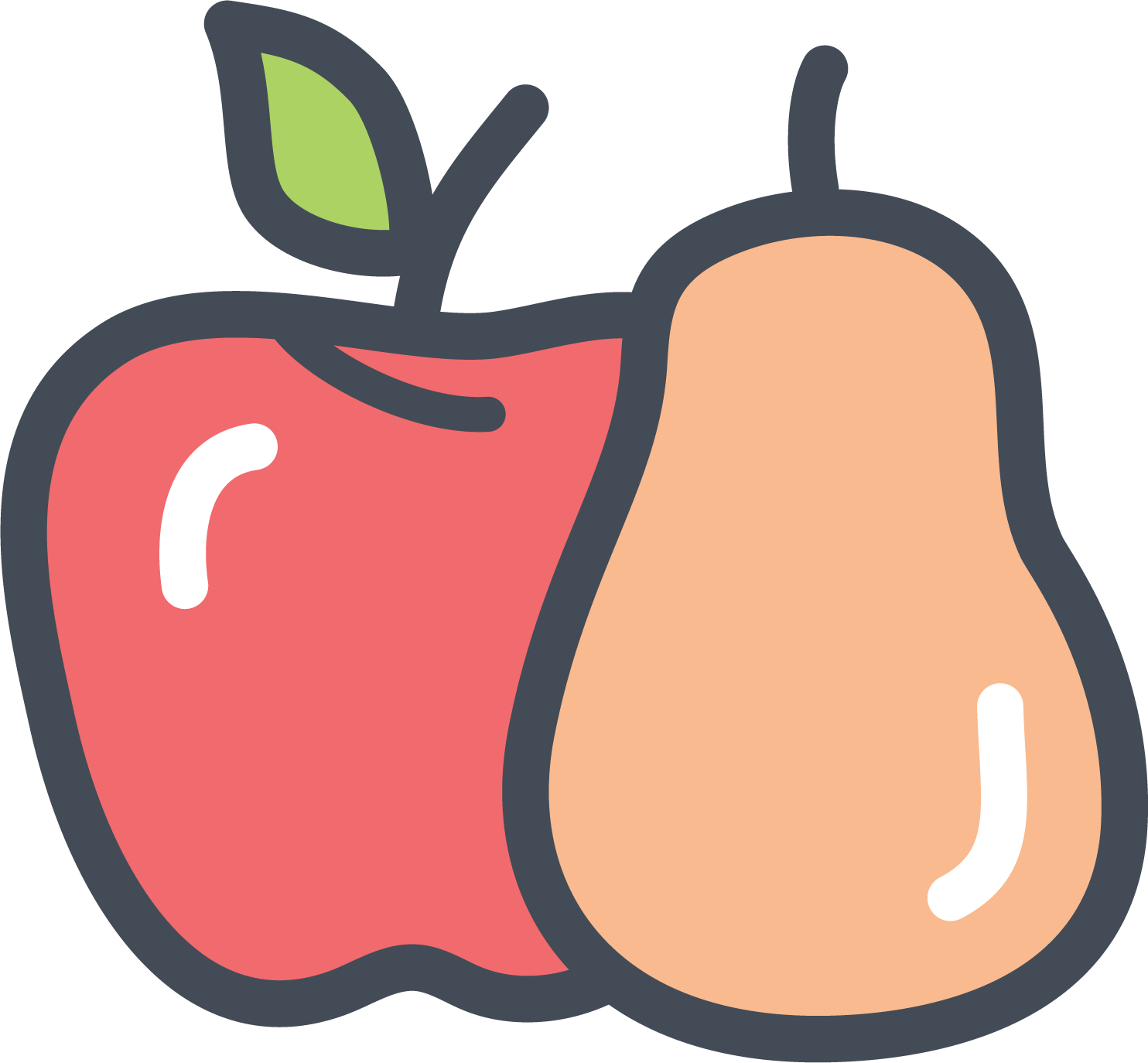
Details
Key Features and Benefits
- Constructed entirely from stainless steel & Acetal co-polymer
- Convenient, detachable infeed for intensive cleaning
- 4 sets of configurable seam crimps
- Auto stoppage function to prevent seal degradation
- Configurable infeed to suit application
- Rotary end-crimp configurable to suit application
- 20 – 400 packs per min.
- 100 product settings
- Pictorial stoppage diagnostics with corrective action pop-ups
Visit Redpack at www.redpack.co.uk for more information.
See all Fox Solutions equipment for advanced automation in fresh produce packaging.
Downloads
Technical Specs
Electrical Requirement
380/440v 50Hz 3Ph N+Earth
380/440v 50Hz 3Ph N+Earth
7 kVA
Circuit Protection
500mA RCD
Pneumatic Requirement
6 Bar minimum dry clean air
Wrapping Materials
OPP or similar
Pack Size (Guide Only)
Maximum Width: 200 mm
Maximum Height: 180 mm (dependent on application)
Max Sealing Width: 280
NB. The Max bag height is determined by the required bag width.
Reel Diameter (mm)
300
Core Diameter (mm)
75
Width (mm)
450 – 650
Machine Speed (ppm)
20 – 400 (dependent upon application)
Noise Emission (dB)
Less than 70 at 1m, 1.6m above floor
Approximate Machine Dimensions
Length (m): 5.5
Width (m): 1.2
Height (m): 1.6
Machine Weight (kg): 1500
About Company
Redpack Packaging Machinery designs and manufactures Flow Wrapping and Packaging Machinery. Our markets include industries such as fresh produce, pharmaceuticals, snack foods, household products, bakery, greeting cards, gifts and toys, etc. With a brand stretching back over 35 years our flow wrapping design follows tried and tested techniques. Despite this, each application brings its own unique requirements for custom-designed features.
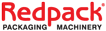
FAQ
A flow wrapping machine, also known as a flow wrapper or horizontal form-fill-seal (HFFS) machine, is a packaging machine used to wrap and seal products in flexible packaging materials. This type of packaging is commonly used for a wide range of food and non-food products. The flow wrapping process involves creating a continuous tube of packaging material around the product, sealing the edges to form a sealed package. Here are key features and aspects of a flow wrapping machine:
- Horizontal Form-Fill-Seal (HFFS) Process:
- Flow wrappers utilize a horizontal form-fill-seal process. The packaging material is unwound from a roll, formed into a tube around the product, filled, and then sealed horizontally.
- Product Feeding:
- Products to be packaged are fed into the flow wrapping machine in a continuous or intermittent manner. The machine accommodates various product shapes and sizes.
- Packaging Material:
- Flow wrappers work with a variety of flexible packaging materials, including clear or printed films. Common materials include polyethylene, polypropylene, and laminates. The choice of material depends on the product and packaging requirements.
- Forming Collar:
- The forming collar is a key component that shapes the packaging material into a tube around the product. It determines the width and length of the package.
- Sealing System:
- Flow wrapping machines feature sealing systems to securely seal the edges of the packaging material, creating a sealed package. Sealing can be accomplished using heat, pressure, or ultrasonic methods, depending on the material and product.
- Adjustable Parameters:
- Operators can adjust various parameters, such as film tension, product spacing, and sealing temperature, to optimize the packaging process for different products.
- Cutting Mechanism:
- A cutting mechanism separates individual packages from the continuous material. The cut is typically made after the sealing process.
- Speed and Efficiency:
- Flow wrappers are designed for high-speed packaging, making them suitable for industries with demanding production requirements. They offer efficient and continuous packaging.
- Versatility:
- Flow wrapping machines are versatile and can handle a wide range of products, including bakery items, snacks, confectionery, fresh produce, frozen foods, hardware, and more.
- Automatic or Semi-Automatic Operation:
- Flow wrappers are available in both automatic and semi-automatic configurations. Automatic machines are fully automated and suitable for high-volume production, while semi-automatic machines may require some manual intervention.
- Product Presentation:
- Flow wrapping provides a neat and visually appealing presentation of products. The clear film allows consumers to see the contents of the package.
- Application in Various Industries:
- Flow wrappers are used in industries such as food and beverage, pharmaceuticals, cosmetics, hardware, and more. They are adaptable to different packaging needs.
- Tamper-Evident Packaging:
- Flow wrapping can provide tamper-evident packaging, enhancing the safety and integrity of the packaged products.
- Integration with Other Equipment:
- Flow wrapping machines can be integrated with other equipment, such as conveyors, labelers, and inspection systems, to create a complete packaging line.
- Customization Options:
- Manufacturers can customize flow wrappers to meet specific product and packaging requirements, including special features or adaptations for unique applications.
A flow wrapping machine is a versatile horizontal form-fill-seal system used for efficient and high-speed packaging of a wide range of products. Its adaptability, speed, and ability to create visually appealing packages make it a popular choice in various industries.
Flow wrapping machines offer several benefits for packaging applications, making them popular in various industries. Here are key advantages of using a flow wrapping machine:
- Versatility:
- Flow wrappers are versatile and can handle a diverse range of products, including bakery items, snacks, confectionery, fresh produce, frozen foods, hardware, and more. This versatility makes them suitable for different industries.
- High-Speed Packaging:
- Flow wrapping machines are designed for high-speed packaging, contributing to increased throughput and efficiency in production lines. This makes them well-suited for industries with demanding production requirements.
- Efficient Material Usage:
- The continuous form-fill-seal process used by flow wrappers minimizes material waste. The packaging material is used efficiently to create sealed packages, reducing the overall packaging costs.
- Clear Product Presentation:
- Flow wrapping provides a clear and visually appealing presentation of products. The transparent or printed film allows consumers to see the contents of the package, enhancing product visibility on the retail shelf.
- Tamper-Evident Packaging:
- Flow wrapping can provide tamper-evident packaging, ensuring the safety and integrity of the packaged products. Sealed edges and clear film make it easy to detect if a package has been tampered with.
- Adaptability to Various Film Types:
- Flow wrappers can work with different types of flexible packaging materials, including polyethylene, polypropylene, laminates, and more. This adaptability allows manufacturers to choose the most suitable material for their products.
- Customization Options:
- Manufacturers can customize flow wrappers to meet specific product and packaging requirements. This includes adjustments for different product sizes, shapes, and packaging styles.
- Integration with Other Equipment:
- Flow wrapping machines can be integrated into complete packaging lines, working seamlessly with other equipment such as conveyors, labelers, and inspection systems. This integration enhances the overall efficiency of the packaging process.
- Reduced Labor Requirements:
- Automatic flow wrappers require minimal manual intervention, reducing the need for labor in the packaging process. This contributes to labor savings and minimizes the risk of human errors.
- Cost-Effective Packaging Solution:
- The efficiency in material usage, high-speed operation, and reduced labor requirements contribute to the overall cost-effectiveness of flow wrapping as a packaging solution.
- Hygienic Design:
- Many flow wrappers are designed with hygiene in mind, featuring easy-to-clean surfaces and meeting industry standards for food and pharmaceutical packaging. This ensures the safety and cleanliness of the packaging environment.
- Wide Range of Applications:
- Flow wrapping machines find applications in various industries beyond food, including pharmaceuticals, cosmetics, hardware, and more. Their adaptability makes them suitable for different packaging needs.
- Easy Changeover and Adjustments:
- Flow wrappers are designed for easy changeover between different product sizes and types. Quick adjustments can be made to accommodate varying packaging requirements.
- Reduced Downtime:
- The efficiency and reliability of flow wrapping machines contribute to reduced downtime in production. This is crucial for maintaining continuous and uninterrupted packaging operations.
The benefits of a flow wrapping machine include versatility, high-speed packaging, efficient material usage, clear product presentation, tamper-evident packaging, adaptability to various film types, customization options, integration with other equipment, reduced labor requirements, cost-effectiveness, hygienic design, a wide range of applications, easy changeover, and reduced downtime. These advantages make flow wrapping a favored packaging solution in many industries.
A flow wrapping machine is versatile and can be used to package a wide variety of food products. Its adaptability makes it suitable for different shapes and sizes of items. Here are examples of types of foods that can be packaged by a flow wrapping machine:
- Bakery Products:
- Bread loaves
- Rolls
- Muffins
- Pastries
- Snack Foods:
- Potato chips
- Pretzels
- Popcorn
- Crackers
- Confectionery:
- Chocolates
- Candy bars
- Gummies
- Hard candies
- Fresh Produce:
- Vegetables (individually wrapped or bundled)
- Fruits (individually wrapped or bundled)
- Frozen Foods:
- Frozen burritos
- Ice cream bars
- Frozen fruit bars
- Dairy Products:
- Cheese slices
- Butter portions
- Yogurt bars
- Meat and Poultry:
- Sausages
- Hot dogs
- Bacon
- Fresh Pasta:
- Packaged pasta
- Stuffed pasta
- Health and Energy Bars:
- Protein bars
- Granola bars
- Nutritional bars
- Dried Fruits and Nuts:
- Raisins
- Almonds
- Trail mix
- Cereal and Granola:
- Breakfast cereal bars
- Granola bars
- Deli Products:
- Deli sandwiches
- Subs
- Pet Treats:
- Dog biscuits
- Catnip treats
- Instant Noodles and Soups:
- Individually wrapped instant noodles
- Soup packets
- Beverages:
- Single-serve drink pouches
- Culinary Ingredients:
- Dried herbs
- Spice blends
- Burgers and Sandwiches:
- Individually wrapped burgers
- Sandwiches
- Popsicles and Ice Cream Novelties:
- Individually wrapped popsicles
- Ice cream sandwiches
- Single-Serve Portions:
- Single-serve portions of condiments
- Single-serve portions of spreads
- Specialty Foods:
- Gourmet chocolates
- Specialty snacks
It’s important to note that the adaptability of flow wrapping machines allows them to handle various shapes and sizes of products. The packaging material used can be adjusted based on the specific requirements of the food product. The clear or printed film used in flow wrapping allows for a visually appealing presentation of the packaged items on retail shelves. Manufacturers can customize flow wrappers to meet the unique packaging needs of different food products.