- Equipment
- P325E
P325E
P325E
Details
Key Features and Benefits
- Precision engineered components housed in a stainless steel fabrication
- 24/7 production capability
- Servo drive system that is simple for operators to use for adjustment to the required bag length and film print position
- 50 product settings that automatically change the bag length, print registration, end crimp slow down, in feed position, machine speed, and printed code and label position
- 20 – 250 packs per min.
- Cantilever design to enhance hygienic cleaning and improve maintenance access
- Quick change product fold box
- Quick release reel handling mechanism
- Three sets of seam crimp rollers – first set cold, second set heated, third set film turnover
- Seam crimp release to prevent film melt when the machine stops
- Rotary end crimp with jaw centers to suit product requirement and knife and anvil with fine adjustment for parallelism
- Precision temperature controllers for the seam crimp and end crimp heaters
- Sealed seam crimp and end crimp electrical slip rings
- End crimp timed stop to prevent film melt when the machine is stationary
- Perforated steel end crimp guarding with gas spring support for operator safety
Visit Redpack at www.redpack.co.uk for more information.
See all Fox Solutions equipment for advanced automation in fresh produce packaging.
Works With
Details
Key Features and Benefits
- Precision engineered components housed in a stainless steel fabrication
- 24/7 production capability
- Servo drive system that is simple for operators to use for adjustment to the required bag length and film print position
- 50 product settings that automatically change the bag length, print registration, end crimp slow down, in feed position, machine speed, and printed code and label position
- 20 – 250 packs per min.
- Cantilever design to enhance hygienic cleaning and improve maintenance access
- Quick change product fold box
- Quick release reel handling mechanism
- Three sets of seam crimp rollers – first set cold, second set heated, third set film turnover
- Seam crimp release to prevent film melt when the machine stops
- Rotary end crimp with jaw centers to suit product requirement and knife and anvil with fine adjustment for parallelism
- Precision temperature controllers for the seam crimp and end crimp heaters
- Sealed seam crimp and end crimp electrical slip rings
- End crimp timed stop to prevent film melt when the machine is stationary
- Perforated steel end crimp guarding with gas spring support for operator safety
Visit Redpack at www.redpack.co.uk for more information.
See all Fox Solutions equipment for advanced automation in fresh produce packaging.
Downloads
Technical Specs
Electrical requirement
380/440v 50HZ 3Ph N+Earth
Electrical consumption
7kVA (16 amps per phase max)
Pneumatic requirement
4 -6 Bar, ISO 8573 -1 Class 6.4.4
Wrapping materials
OPP, Heat sealing
laminates, Cold seal, Paper
End crimp shaft centres (mm) 1
108 126 156 186
Length (mm)
130-340 150-400 180-490 215-580
Width (mm)
20-250
Height (mm)
1-60 1-75 30-105 30-138
Reel diameter (mm)
320 (max)
Core diameter (mm)
75
Width (mm)
650/850
Machine speed (ppm)
20 – 450 ppm
(Dependent on application)
Noise emission
Less than 70dBa at 1m
distance, 1.6m above floor.
Approx. wt. (kg)
800
About Company
Redpack Packaging Machinery designs and manufactures Flow Wrapping and Packaging Machinery. Our markets include industries such as fresh produce, pharmaceuticals, snack foods, household products, bakery, greeting cards, gifts and toys, etc. With a brand stretching back over 35 years our flow wrapping design follows tried and tested techniques. Despite this each application brings its own unique requirements for custom designed features.
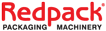
FAQ
A Horizontal Flow Wrapping machine is a packaging machine used in the food, pharmaceutical, and other industries to wrap products in a continuous film of packaging material, typically plastic. The machine creates a horizontal flow of the packaging material, forming a tubular shape around the product, and then seals the edges to create a tightly wrapped package.
Here’s a breakdown of the key features and functions of a Horizontal Flow Wrapping machine:
- Product Feeding: Products are fed onto the machine’s conveyor belt, where they are aligned in a single file.
- Film Unwinding: The packaging material, usually a roll of plastic film, is unwound and formed into a tubular shape around the products.
- Product Encasement: The products move through the tubular film, and the machine seals the edges of the film to encase each individual product.
- Sealing: The sealing process ensures that the packaging material is securely sealed around the product to protect it from external factors such as contamination, moisture, and damage.
- Cutting: After sealing, the continuous tube of wrapped products is cut into individual units or a specified length.
- End Seal: The machine forms end seals on both sides of each wrapped product, creating a complete and sealed package.
- Discharge: The wrapped products are then discharged from the machine for further processing, such as labeling, boxing, or distribution.
Horizontal Flow Wrapping machines are versatile and can handle a variety of products, including food items like candy bars, cookies, and fresh produce, as well as non-food items such as pharmaceuticals, toiletries, and household goods. They are known for their efficiency in high-speed packaging lines and contribute to the automation of the packaging process.
Horizontal Flow Wrapping machines offer several benefits, making them popular in various industries for packaging a wide range of products. Here are some key advantages:
- Versatility: Horizontal Flow Wrapping machines are versatile and can handle different types of products, including food items, pharmaceuticals, cosmetics, and more. They can accommodate various shapes and sizes, making them suitable for a diverse range of applications.
- High Speeds: These machines are designed for high-speed packaging, making them ideal for large-scale production lines. The continuous flow and automation contribute to increased efficiency and productivity.
- Sealing Quality: Horizontal Flow Wrapping machines provide consistent and reliable sealing. This ensures that the products are securely wrapped, protecting them from external elements such as moisture, contaminants, and damage during transportation and storage.
- Film Savings: The design of these machines allows for efficient use of packaging material. The continuous film is precisely tailored to the size of each product, minimizing waste and contributing to cost savings in terms of packaging material.
- Ease of Integration: Horizontal Flow Wrapping machines can be easily integrated into existing production lines or combined with other packaging equipment. This flexibility allows manufacturers to optimize their overall packaging processes.
- Visibility and Presentation: The horizontal flow wrapping process often results in a clear, unobstructed view of the product through the packaging. This enhances the product’s visibility and presentation on store shelves, attracting consumers with an appealing appearance.
- Extended Shelf Life: The sealed packaging created by Horizontal Flow Wrapping machines helps extend the shelf life of perishable products by providing a protective barrier against external factors such as air, moisture, and contaminants.
- Reduced Labor Costs: Automation in the packaging process reduces the need for manual labor, leading to cost savings in terms of labor expenses and increased overall efficiency.
- Customization Options: These machines offer options for customization, allowing manufacturers to choose specific features, such as different types of seals or printing capabilities for branding and labeling.
- Compliance with Industry Standards: Horizontal Flow Wrapping machines are designed to meet industry standards and regulations for food safety and product integrity, ensuring that the packaged products meet the required quality and safety standards.
Overall, Horizontal Flow Wrapping machines contribute to improved efficiency, cost-effectiveness, and product presentation in the packaging industry.
A Horizontal Flow Wrapping machine is versatile and can be used to package a wide variety of foods. Here are some examples of foods that can be effectively packaged using this type of packaging machinery:
- Bakery Products:
- Bread and rolls
- Biscuits and cookies
- Cakes and pastries
- Confectionery:
- Chocolate bars
- Candy and sweets
- Chewing gum
- Snack Foods:
- Potato chips
- Pretzels
- Nuts and dried fruits
- Fresh Produce:
- Fresh fruits (individually or in sets)
- Vegetables (when pre-packaged)
- Dairy Products:
- Cheese portions
- Single-serving yogurt cups
- Frozen Foods:
- Ice cream bars
- Frozen desserts
- Meat and Poultry:
- Sliced deli meats
- Sausages
- Pre-packaged Meals:
- Ready-to-eat meals
- Sandwiches and wraps
- Cereal and Granola Bars:
- Single bars or multipacks
- Health and Nutrition Bars:
- Protein bars
- Energy bars
- Pet Food:
- Individual portions or multipacks
- Beverages:
- Single-serving drink pouches
It’s important to note that the suitability of a Horizontal Flow Wrapping machine for a particular food product depends on factors such as the product’s size, shape, and packaging requirements. Additionally, the machine can be configured with specific features to accommodate the unique characteristics of different food items. Manufacturers often customize these machines to meet the specific needs of their products and packaging goals.